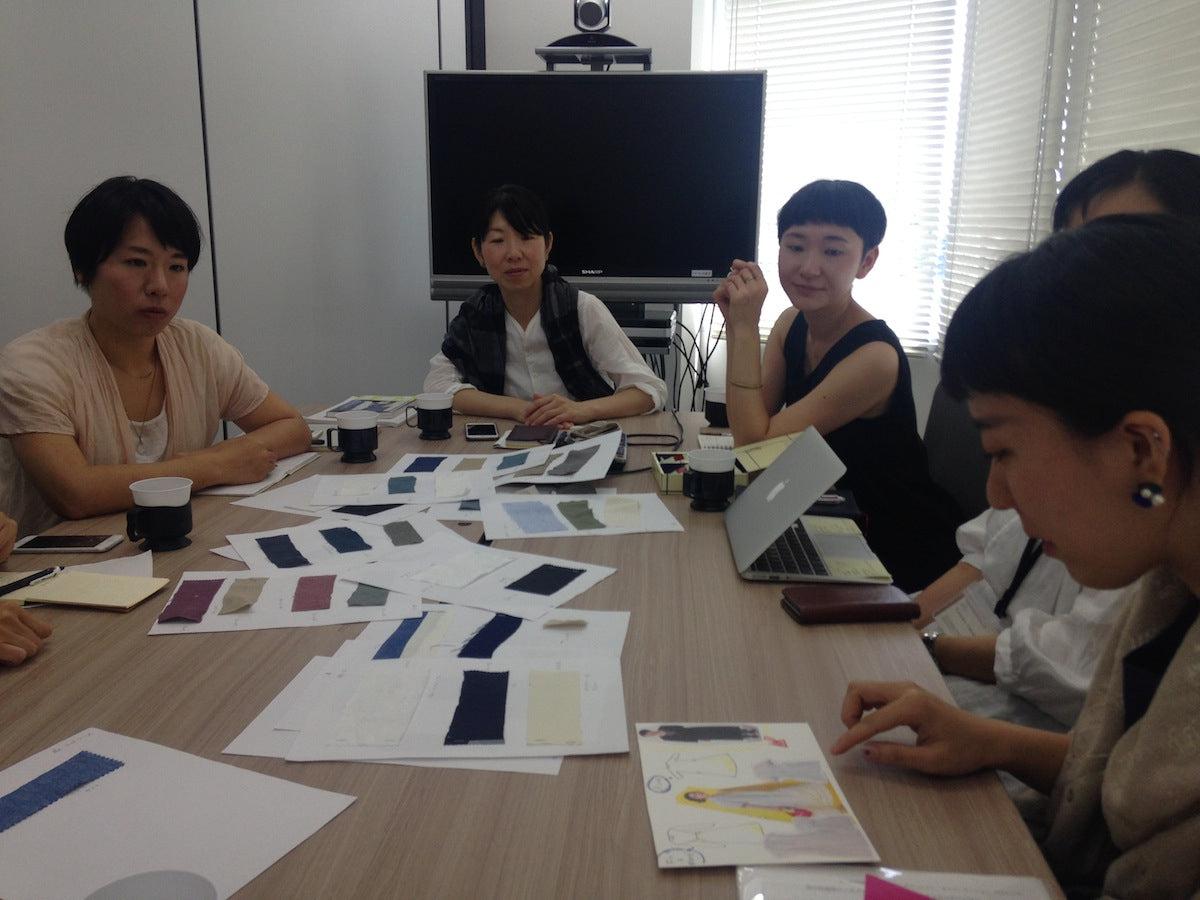
Kagure no Wardrobe #01 kicked off last month, but after a month's break, we held our second planning meeting.
Kagure no Wardrobe #01 (previous report)
2016/7 #01-1 REPORT ~Examination of production items~
Last time, we went back to Kagure's concept and shared and confirmed the concept and positioning of Kagure's original product series "Kagure's Wardrobe". On top of that, I thought about what to make for this project, which will be the first item in Kagure's wardrobe, and decided on a dress. A one-piece dress that can be matched with Kagure's original shop coat. Made of natural materials, it can be worn elegantly even if an adult woman wears it alone. I solidified the image of such a big atmosphere.
Over the past month, Kagure has given us a concrete image of how to make a dress. There are various methods, such as clothes that you usually like, clothes that are handled by Kagure, magazines, photos, and shape images. Mr. Machida from enrica prepared the fabric after receiving the result of the last meeting.
This time, based on these image sources and many fabric samples, we will consider the actual specifications of the clothes.
Kagure no Wardrobe #01 (previous report)
2016/7 #01-1 REPORT ~Examination of production items~
Last time, we went back to Kagure's concept and shared and confirmed the concept and positioning of Kagure's original product series "Kagure's Wardrobe". On top of that, I thought about what to make for this project, which will be the first item in Kagure's wardrobe, and decided on a dress. A one-piece dress that can be matched with Kagure's original shop coat. Made of natural materials, it can be worn elegantly even if an adult woman wears it alone. I solidified the image of such a big atmosphere.
Over the past month, Kagure has given us a concrete image of how to make a dress. There are various methods, such as clothes that you usually like, clothes that are handled by Kagure, magazines, photos, and shape images. Mr. Machida from enrica prepared the fabric after receiving the result of the last meeting.
This time, based on these image sources and many fabric samples, we will consider the actual specifications of the clothes.
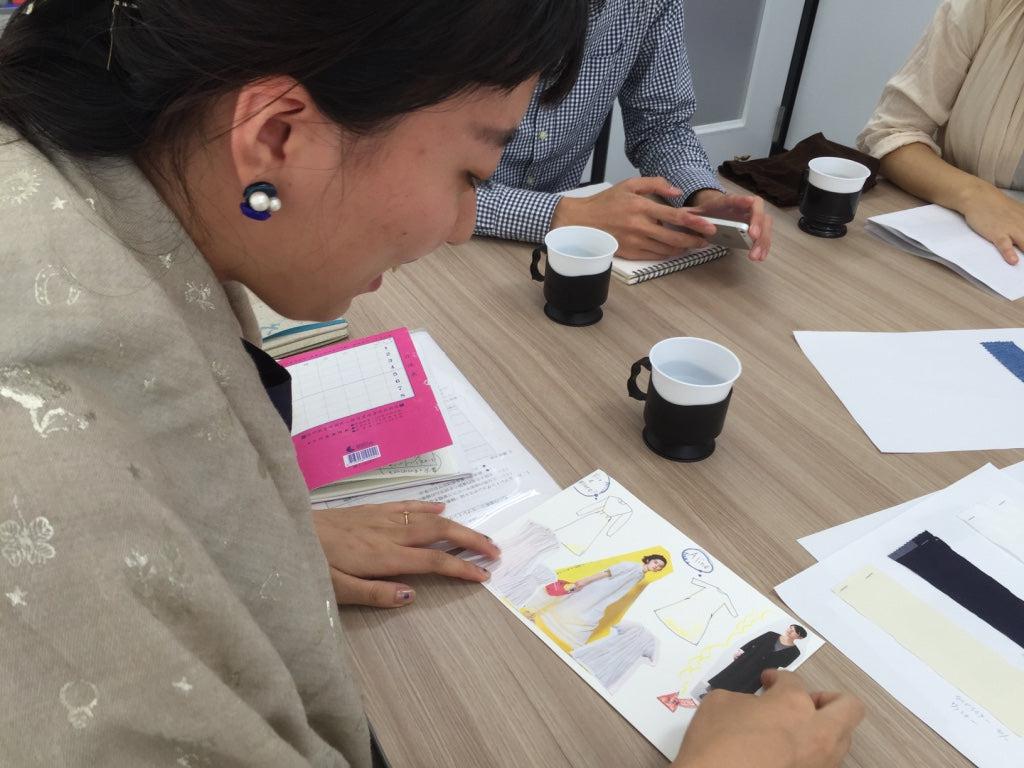
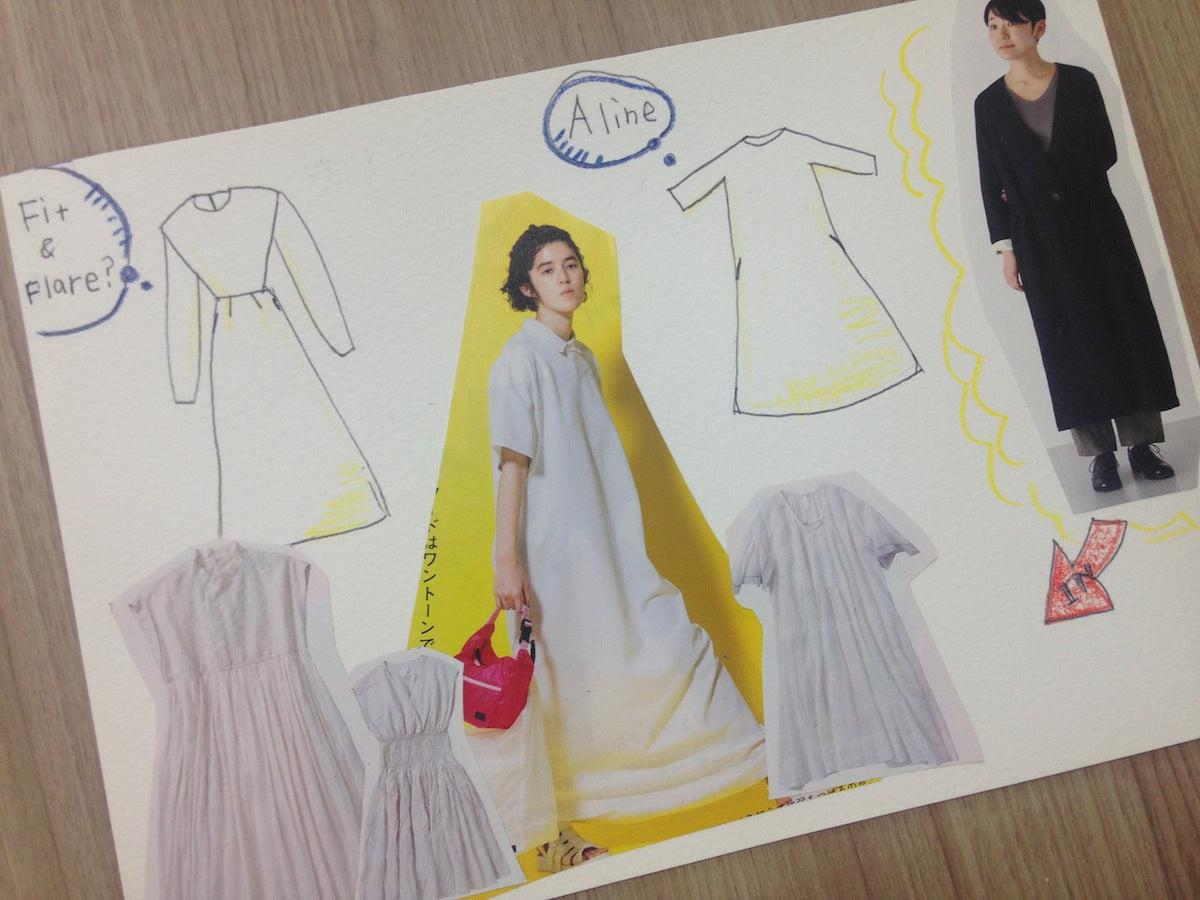
This board was prepared by Mr. Moro (Marunouchi store). Photos and illustrations, like a page in a magazine. While imagining how to interact with customers who come to the store, we have expanded the image of how we would like to introduce the coordination with the shop coat, the silhouette line, and how to introduce it. The power of illustration and design is strong. It was a meeting with 8 people, but with this one board, the density of the air increased a lot.
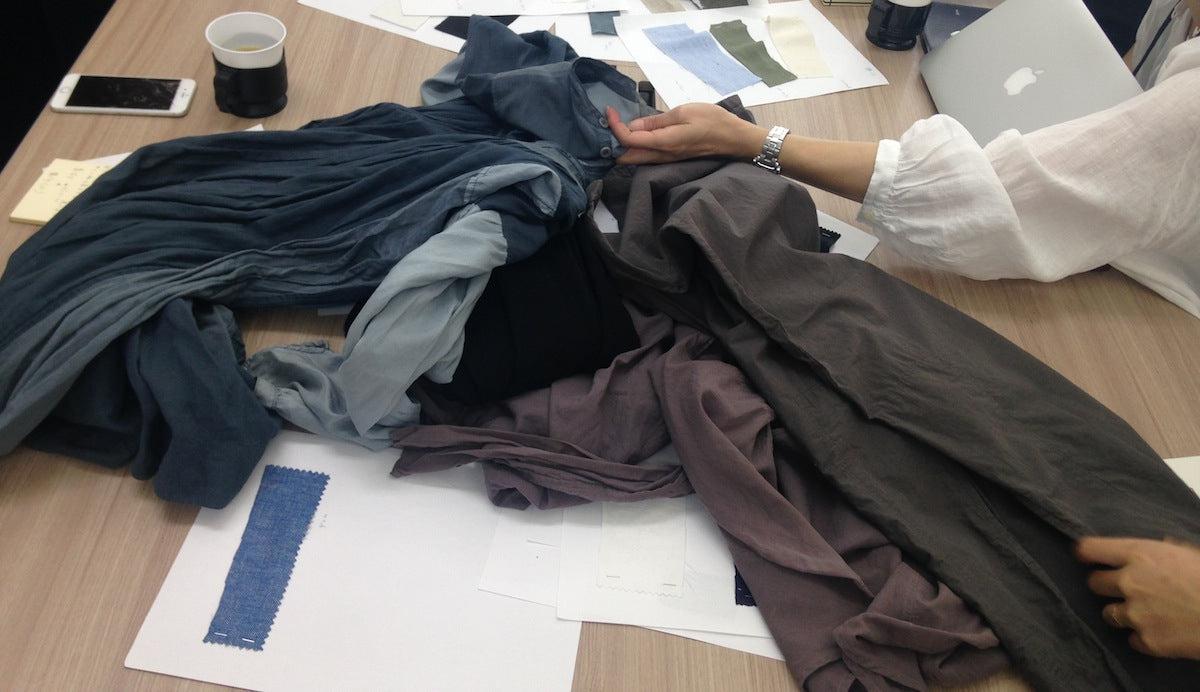
Mr. Okuda (Omotesando store) and Mr. Yazawa (Midtown store) brought clothes that they usually wear. Points that are excellent or interesting when actually worn, compatibility between fabric and shape, etc. When creating something tangible, the image that can be shared with words alone is limited. The clothes you brought are also fashionable.
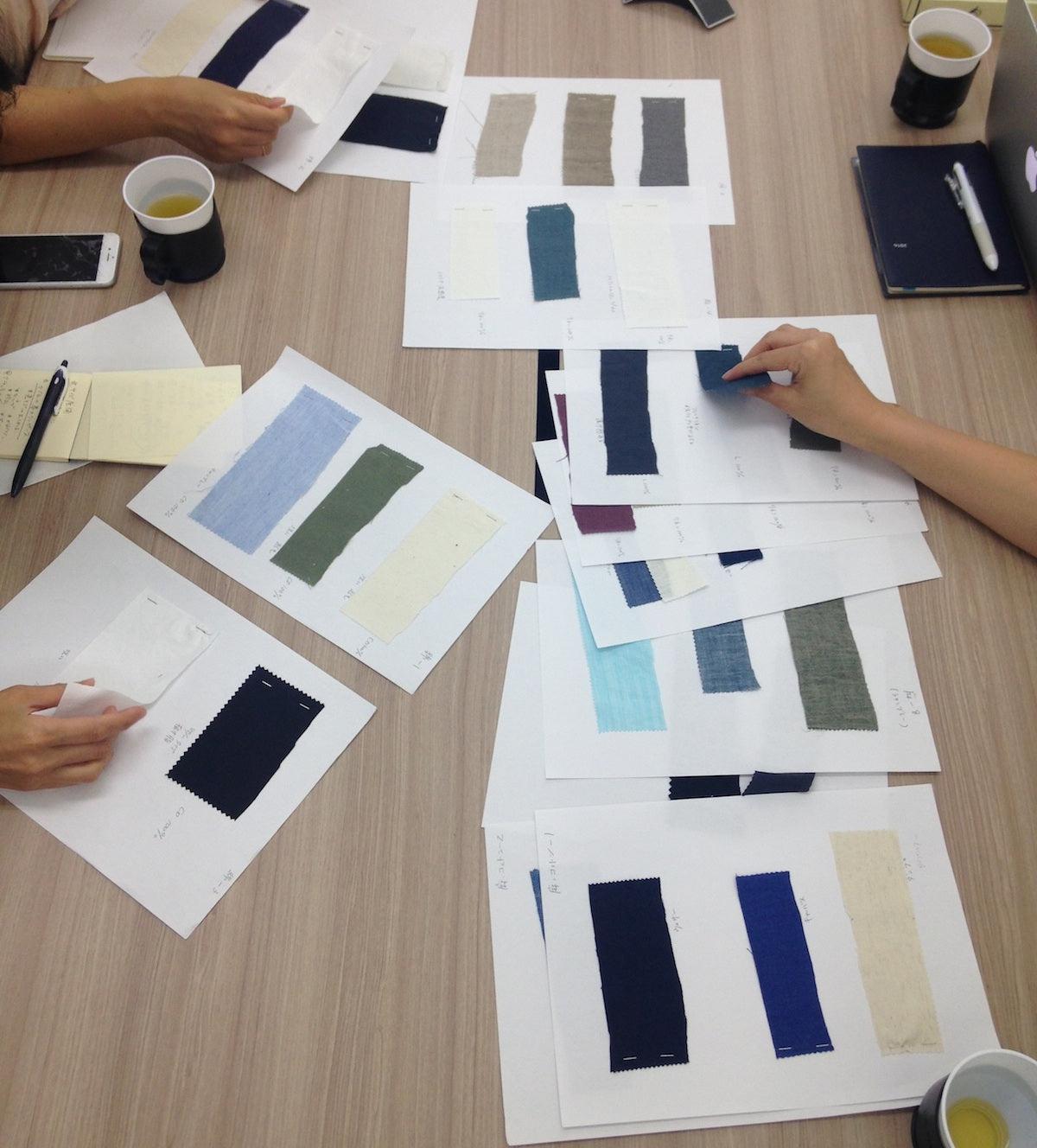
And from enrica machida, a lot of fabric samples. We have prepared a variety of fabrics with different materials, thread thickness, weave density, and processing types, and we have selected and prepared materials from elegant to casual. In my previous job, I accompanied Mr. Machida to procure fabrics. Sorting is a tough job.
In the later stage of dyeing, I touch the fabric sample and expand my imagination while comparing it with other image sources.
In the later stage of dyeing, I touch the fabric sample and expand my imagination while comparing it with other image sources.

Keywords and images come to mind while looking at and touching the collected materials.
If you line up fragmentary keywords, you will not be able to narrow it down to one form and it will only swell, but as a concept and theme to return to this time,
● Make what Kagure should make as an original product
●What kind of things do we create? How do you want to convey that to your customers?
That means. From the root part, get a little closer to the clothes,
●You can wear it elegantly even by itself
●You can wear it with a shop coat or a long coat.
I went back over and over again and narrowed it down little by little.
If you line up fragmentary keywords, you will not be able to narrow it down to one form and it will only swell, but as a concept and theme to return to this time,
● Make what Kagure should make as an original product
●What kind of things do we create? How do you want to convey that to your customers?
That means. From the root part, get a little closer to the clothes,
●You can wear it elegantly even by itself
●You can wear it with a shop coat or a long coat.
I went back over and over again and narrowed it down little by little.
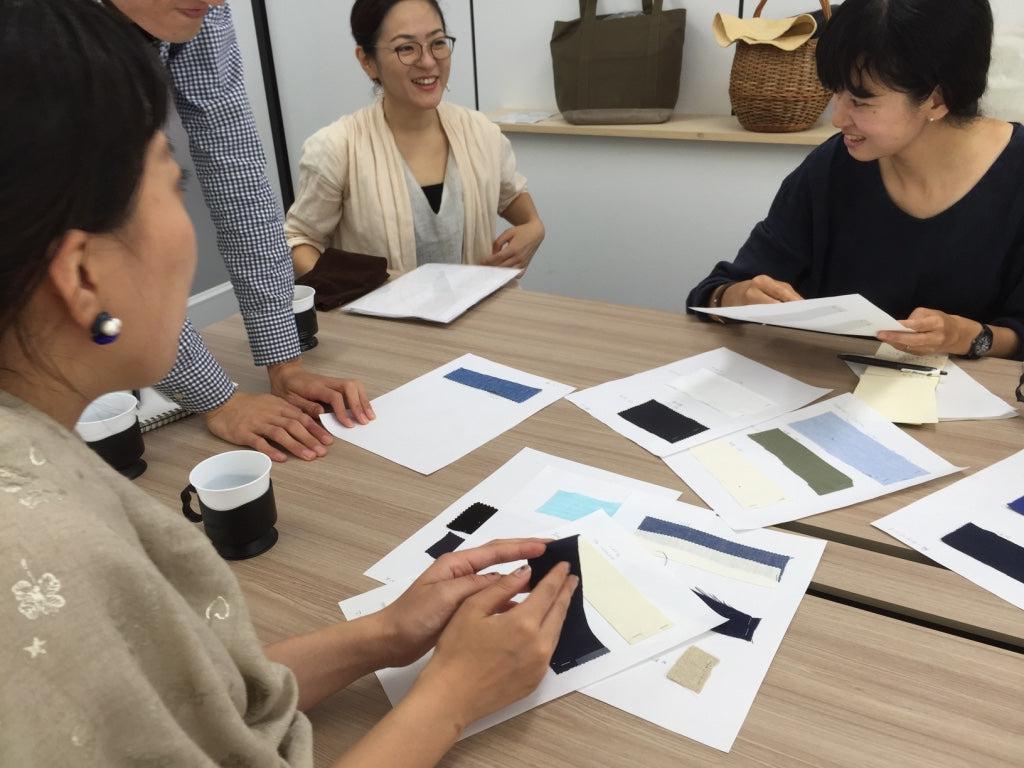
How do you apply this concept to your clothes? This is the biggest hurdle, but with the advice and progress of enrica Machida, we will make strong progress.
“What do you need to look stylish with just one piece?”
“How do you create femininity and femininity?”
Although it's a sensory area, such as the sense of omission and how to add sharpness, he explained it in an easy-to-understand manner with specific examples. It's as if the designer's mind is opened and shown how the image is transformed into the design and shape of the clothes.
Once again, the real pleasure of this project is that we can share the knowledge of professionals and move forward together. Machida-san, thank you very much.
The words that struck me personally the most were:
"For a simple form to look good, you have to make it right."
I usually work with craftsmen to think and make tableware instead of clothes, but it was also common. Just because something looks simple doesn't mean it's easy to make. Because it is simple, it is a feeling that deception does not work and the depth of investigation is deep. Also, it may be easy to copy the shape, but the materials are not exactly the same. It becomes a thing.
Although we borrowed the power of Mr. Machida for the patterns and designs, of course, we are all prepared to pursue “properly making” Kagure originals, and our hearts are one.
While showing me how to think about clothing design, we all thought about the fabric selection, length, silhouette, and detailed specifications. Don't be a half-hearted landing while thinking about balance.
For example, even if you put the same gathers in the same volume, the impression you give will be different depending on the fabric and how much space there is in the collar. It is not completed by splicing each detail, but is made up of balance and harmony with the whole. That's why there are limitless patterns and designs, and there are things that come to mind and things that don't.
A luxurious time to learn while actually having a planning meeting for manufacturing. Every time, this time was also a lot of learning.
“What do you need to look stylish with just one piece?”
“How do you create femininity and femininity?”
Although it's a sensory area, such as the sense of omission and how to add sharpness, he explained it in an easy-to-understand manner with specific examples. It's as if the designer's mind is opened and shown how the image is transformed into the design and shape of the clothes.
Once again, the real pleasure of this project is that we can share the knowledge of professionals and move forward together. Machida-san, thank you very much.
The words that struck me personally the most were:
"For a simple form to look good, you have to make it right."
I usually work with craftsmen to think and make tableware instead of clothes, but it was also common. Just because something looks simple doesn't mean it's easy to make. Because it is simple, it is a feeling that deception does not work and the depth of investigation is deep. Also, it may be easy to copy the shape, but the materials are not exactly the same. It becomes a thing.
Although we borrowed the power of Mr. Machida for the patterns and designs, of course, we are all prepared to pursue “properly making” Kagure originals, and our hearts are one.
While showing me how to think about clothing design, we all thought about the fabric selection, length, silhouette, and detailed specifications. Don't be a half-hearted landing while thinking about balance.
For example, even if you put the same gathers in the same volume, the impression you give will be different depending on the fabric and how much space there is in the collar. It is not completed by splicing each detail, but is made up of balance and harmony with the whole. That's why there are limitless patterns and designs, and there are things that come to mind and things that don't.
A luxurious time to learn while actually having a planning meeting for manufacturing. Every time, this time was also a lot of learning.
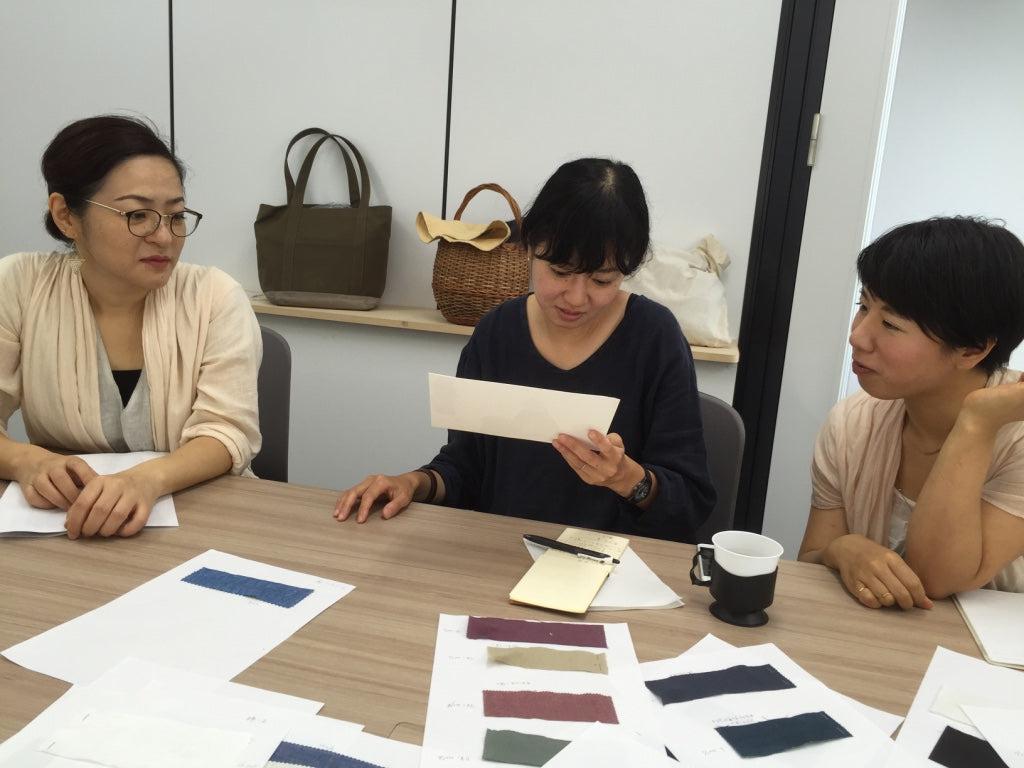
Two hours of talking like this. Rough design specifications and fabrics have been decided.
・The fabric has been narrowed down to several patterns (linen, cotton)
・ A dress with a silhouette that falls down with a stone instead of a shirt type
It's hard to convey the degree of progress compared to the last time when I write it, but don't worry. The fabric is also squeezed, the shape is more concrete, and it is slowly progressing.
The next (3rd time) will be on 9/13.
For the fabric, check the dyeing pattern of the fabric that remained as a candidate this time. In addition, Mr. Machida will search for new good fabrics based on the fabric candidates this time. Also, for the shape, we will ask you to make a toile (a shape sample made with sheeting), and we will work out the specifics of the shape based on this.
At the same time as the fabric, it will be a tangible first step before the 1st sample. I'm looking forward to how it will go next and how it will change (?).
Kagure's original dress, planned and produced over a period of more than half a year. This project is to deliver a report on the product planning of clothes making from scratch. Out of 4-5 times, the 2nd time is over. Considering the amount of work to be done in the future, qualitatively, it is about the second stage. From now on, I will think closer to the shape of clothes. Through this project report, please take a look at how one piece of clothing is made.
Here is the upcoming schedule ↓
//////////////////////////////////////////////////// //////
[Kagure no Wardrobe #01 Schedule]
2016/7 #01-1 REPORT ~Examination of production items~ <End>
2016/8 #01-2 ~ Consideration of production items ~ <This time>
2016/9 #01-3 〜Toilet Check・Fabric Examination〜 <Next time>
2016/10 #01-4 ~1st sample check~
2016/11 #01-5 ~2nd sample check~
2016/12 final decision
2017/1~2 production
Released March 2017
*Next time onwards is planned. Subject to change.
//////////////////////////////////////////////////// //////
・The fabric has been narrowed down to several patterns (linen, cotton)
・ A dress with a silhouette that falls down with a stone instead of a shirt type
It's hard to convey the degree of progress compared to the last time when I write it, but don't worry. The fabric is also squeezed, the shape is more concrete, and it is slowly progressing.
The next (3rd time) will be on 9/13.
For the fabric, check the dyeing pattern of the fabric that remained as a candidate this time. In addition, Mr. Machida will search for new good fabrics based on the fabric candidates this time. Also, for the shape, we will ask you to make a toile (a shape sample made with sheeting), and we will work out the specifics of the shape based on this.
At the same time as the fabric, it will be a tangible first step before the 1st sample. I'm looking forward to how it will go next and how it will change (?).
Kagure's original dress, planned and produced over a period of more than half a year. This project is to deliver a report on the product planning of clothes making from scratch. Out of 4-5 times, the 2nd time is over. Considering the amount of work to be done in the future, qualitatively, it is about the second stage. From now on, I will think closer to the shape of clothes. Through this project report, please take a look at how one piece of clothing is made.
Here is the upcoming schedule ↓
//////////////////////////////////////////////////// //////
[Kagure no Wardrobe #01 Schedule]
2016/7 #01-1 REPORT ~Examination of production items~ <End>
2016/8 #01-2 ~ Consideration of production items ~ <This time>
2016/9 #01-3 〜Toilet Check・Fabric Examination〜 <Next time>
2016/10 #01-4 ~1st sample check~
2016/11 #01-5 ~2nd sample check~
2016/12 final decision
2017/1~2 production
Released March 2017
*Next time onwards is planned. Subject to change.
//////////////////////////////////////////////////// //////