Indigo Dyed Linen Furoshiki Square
Couldn't load pickup availability
- # 60番手薄手リネン生地
- # ネコポス配送1個まで
- # 亜麻(リネン)
- # 受注製作
- # 四角布
- # 本藍染め
- # 風呂敷
- # 麻
[Made-to-order] We will manufacture after receiving an order. After confirming your order and payment, it will take about 1 month.
* * *
Furoshiki made from the same fabric as PINT linen handkerchiefs is dyed with genuine indigo tie-dye.
Furoshiki is often made of crepe, cotton or synthetic fiber, but when I saw the shiny and taut linen fabric used in PINT, I was born with the desire to create a large-sized furoshiki that brings out the texture and pattern. It's a thing. The size is 90 cm square, so it is a size that can be used firmly when traveling or carrying luggage. The fabric is thin and not bulky, so it has a user-friendly finish that is "big and small". As the name furoshiki suggests, there is no limit to how you can use it. Wrap, hang, spread, wipe, cover, use anything. A thin, large square. I feel that furoshiki is a really excellent one among many cloths and tools. In addition to the freedom of use, it is also portable, and personally I have the most respect for it.
At work, when I carry a lot of products, I wrap them up in small bags, or wrap a single item in place of cushioning material. When traveling, it can be used to wrap a change of clothes, and if it is made of linen material, it can also be used as a towel at the gym or in the bath. At the store, you can hang it and decorate it or hang it.
I personally use it roughly, but of course, there are many ways to tie it and use it like a bag or wrap it as a gift. However, even if you don't have such a knotting technique, just wrapping it and tying it like a string will be enough. (I also think that it is best to wrap it with a thin large cloth because the knot becomes bulky when tied.)
It's a very fun tool, so even if you've never used it before, please give it a try.
The dyer is Yukari Saka, who trained in Tokushima, the home of indigo dyeing.
Indigo dyeing is a technique that has remained unchanged since the Edo period, called Tennen Aku Hakkodate. Sukumo, which is fermented indigo, and wheat gluten are used to make a dye solution in an indigo vat. This dye solution is checked daily by sight, smell, touch, and sometimes by licking it, and it is stirred to promote fermentation and continue to be adjusted.
It is said that the deep and beautiful colors unique to genuine indigo dyeing come out because various organic substances are mixed in this dye solution. Dyeing is carried out from spring to autumn when the temperature is high and fermentation progresses.
The fabric or product to be dyed is soaked in this indigo vat, and then kneaded so that it is well blended with the fabric. The color does not appear in the dyeing liquid of the indigo vat, but the color comes in when exposed to the air and oxidized. Unlike chemical dyes, the color does not appear in one go, so this process is repeated several times a day for one to two weeks. In this way, the color is fixed by repeatedly dyeing over time and times.
If the fabric is immersed in the dye solution as it is, it becomes plain, but a pattern is added using a technique called shibori. Shibori involves pre-processing the fabric by folding it, tying it, and threading it with a needle before soaking it in the indigo vat and then dipping it in the dye solution. Depending on the shape of the pre-processing of the fabric, it is divided into areas where dye enters and areas where dye does not enter, and this becomes the tie-dye pattern. Since there is no pattern, there are no clear boundaries between colors, and everything becomes a gradation. From white to dark blue, the colors that overlap with various indigo colors are really beautiful.
This pattern uses the same shibori technique as the Yamaji pattern. By changing the angle and placement, it is dyed into a square pattern.
It is said that this indigo dyeing is not just a simple indigo color, but a mixture of various colors such as red and green. When you actually look at it in the sunlight or shake it, it looks reddish, blackish, and purple, giving it a rich look. Vegetable dyeing is also said to reflect bright colors due to diffused reflection, and this is the appeal of natural dyeing.
Dyed furoshiki uses the same fabric as linen handkerchiefs. Furoshiki is sewn in three rolls. Natural dyes don't dye synthetic threads, so I use cotton threads for sewing.
The creator of the linen fabric is a craftsman who has a thorough knowledge of linen materials and weaves, who has inherited the tradition of Omi Jofu in Shiga Prefecture's Omi Koto production area and currently mainly manufactures fabrics for apparel collection brands.
Compared to the rapier looms that are mainly used today, the production speed is much slower, but the density and texture of the fabric can only be achieved with shuttle looms.
Since linen tends to break when a force is applied to it while it is being woven on a loom, the threads will break during the weaving process, and the threads will be tied one by one by hand as the work progresses.
Weaving with this shuttle loom requires not only skill, but also perseverance and time. Thick and durable threads such as cotton denim and canvas are still woven with shuttle looms, but 100% linen fabrics made with shuttle looms are rare.
This is what is called the shuttle, through which the weft thread is passed through the shuttle loom.
It is made of heavy wood and moves back and forth from side to side to pass the weft threads. Its movement is like a satellite, so it is called a shuttle (satellite). On the other hand, modern rapier looms are designed to fly the weft with an air jet. Even with this difference alone, I think you can imagine the difference in speed.
Linen is difficult to handle when weaving, and thin threads are particularly easy to cut, making fabric production more difficult.
This fabric is woven with high density using 60 thread, which is often used for shirts and other thin threads. When you think of linen, you may have an image of a slightly uneven thread, but you can see that it is a straight and beautiful thread. The work of the process of making yarn called spinning is reflected here. If the thread is bad, it is difficult to weave it tightly and densely, so it is necessary to ensure that the quality of the entire process is consistent. The high-density weave prevents fluff from standing up, and the use of plenty of threads also increases water absorption. Also, the combination of fine threads and high density creates a smooth texture.
Due to the characteristics of linen fibers, especially in the case of fine counts, it does not produce straight threads like synthetic fibers or cotton, but there are few neps, etc., resulting in beautiful threads and woven fabrics.
The indigo color is firmly contained in the fine thread fabric, and there is also a luster unique to linen.
Dyed with the fabric, it was a very good match and I was able to multiply it well. Since indigo dye has a dark color, you can use it without worrying about it getting dirty. The more you use it, the softer the fabric will be, and the dyed color will look more mature. I want you to use it for a long time and grow it.
【material】
100% linen
Indigo dyeing (natural lye fermentation)
【size】
90×90cm
Since the product is dyed, there is some shrinkage and there is a slight difference.
[exterior]
none
[Handling and care]
For the first few times, run water first or wash separately from normal laundry to prevent color transfer. In the case of genuine indigo dyeing, it is rare that the color fades as much as the so-called denim. Due to strong friction, etc., the color may transfer, but if it is within the range of use as a furoshiki, you can use it without problems. Even if the color is transferred, it is often washed off.
Please use a neutral detergent for washing. Please avoid using dryers, bleaches, fabric softeners, fluorescent brighteners, etc., as they are likely to cause discoloration and significant changes in the texture of the fabric. In order to prevent color transfer due to friction during dehydration, we recommend using a laundry net when using a washing machine.
It is vulnerable to long-term sunlight exposure and is prone to discoloration, so please dry it in the shade after washing. In addition, fluorescent lights may cause fading, so when storing for a long period of time, we recommend storing in a place that is not exposed to light.
When ironing, it is recommended to use a medium or lower heat setting instead of a high setting. When setting the high temperature, apply a pressing cloth.
*Frequently Asked Questions/Supplementary Comments*
・There are other types of patterns for this indigo-dyed furoshiki. There is also a handkerchief.
・We used to use organic linen fabric, but it became difficult to procure the raw material for the yarn, and we are no longer able to continue using it. We use fabrics with the same count, thickness and color, but with non-organic yarns.
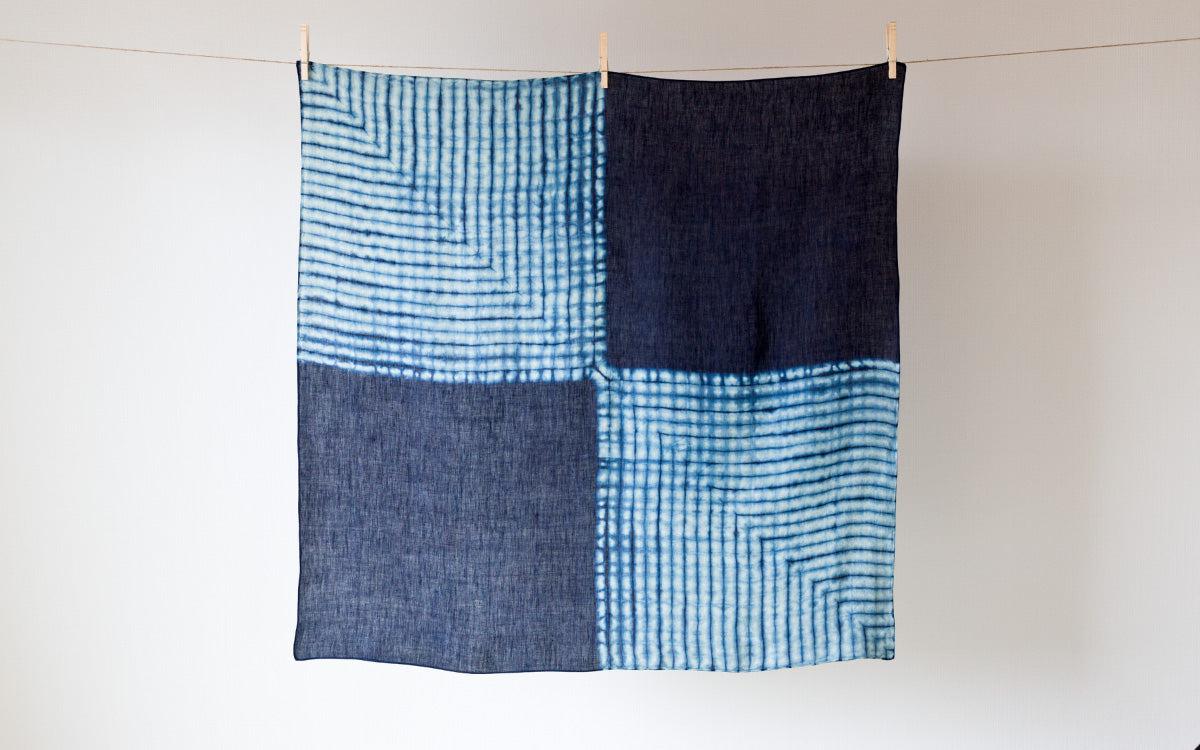
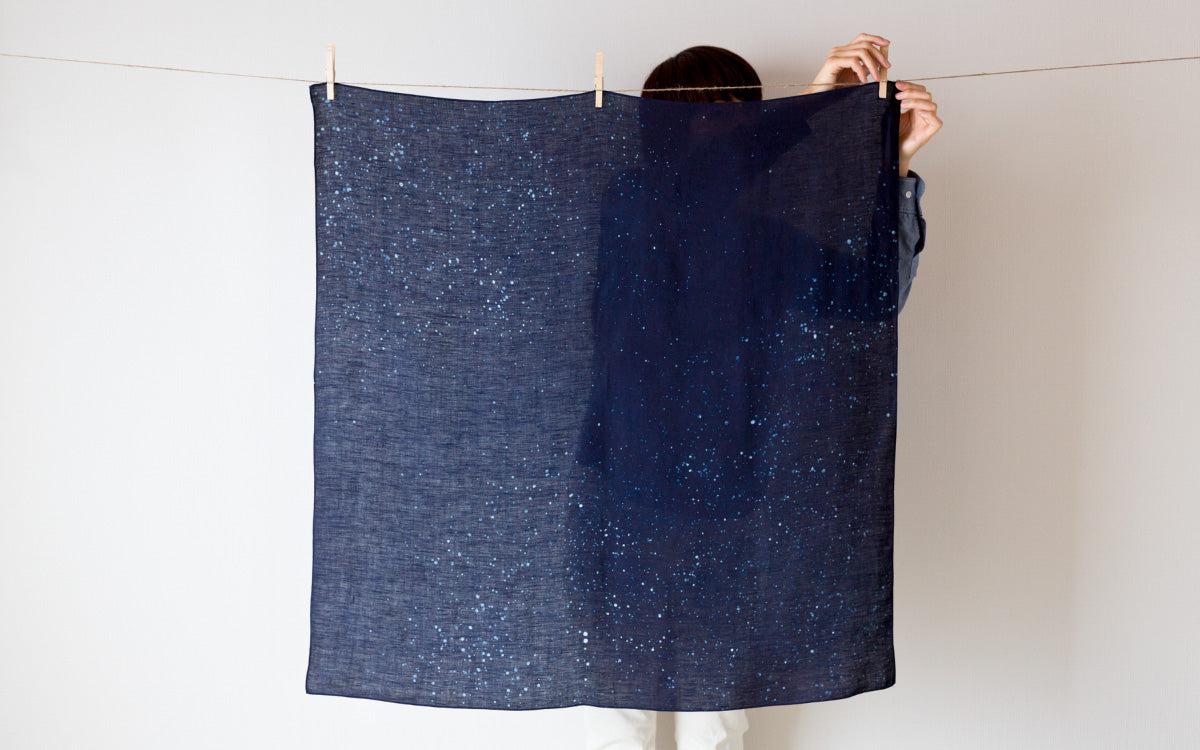

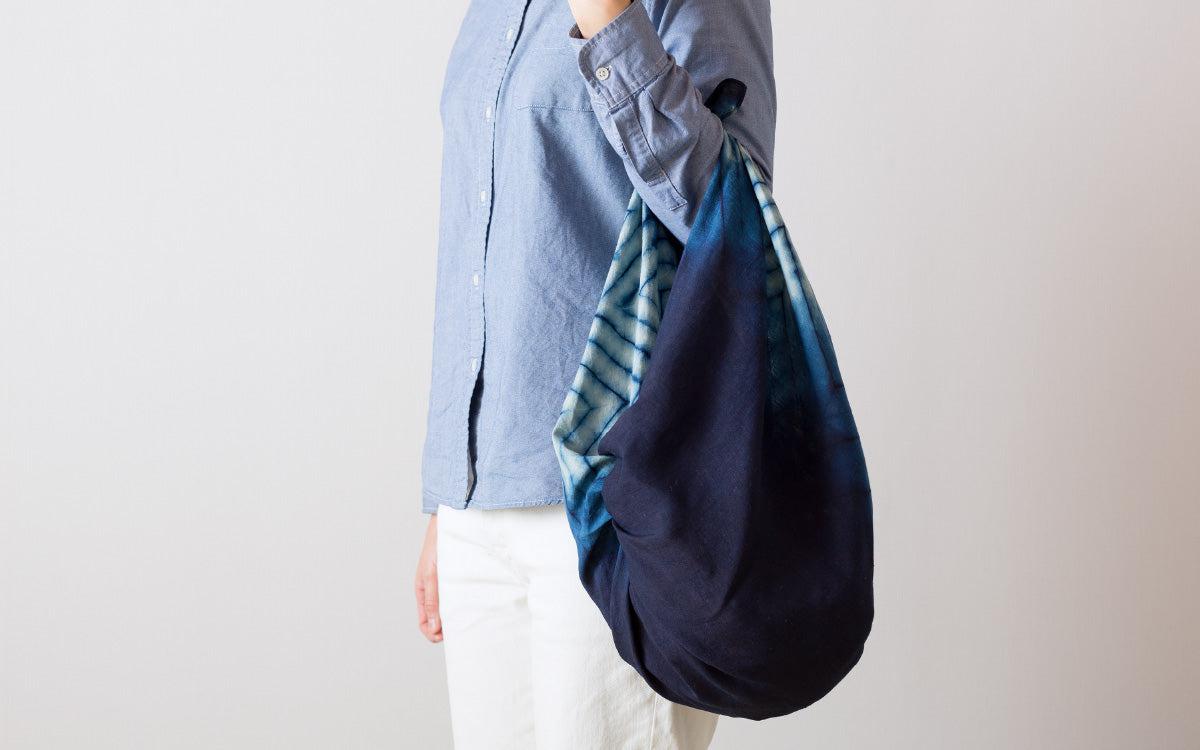
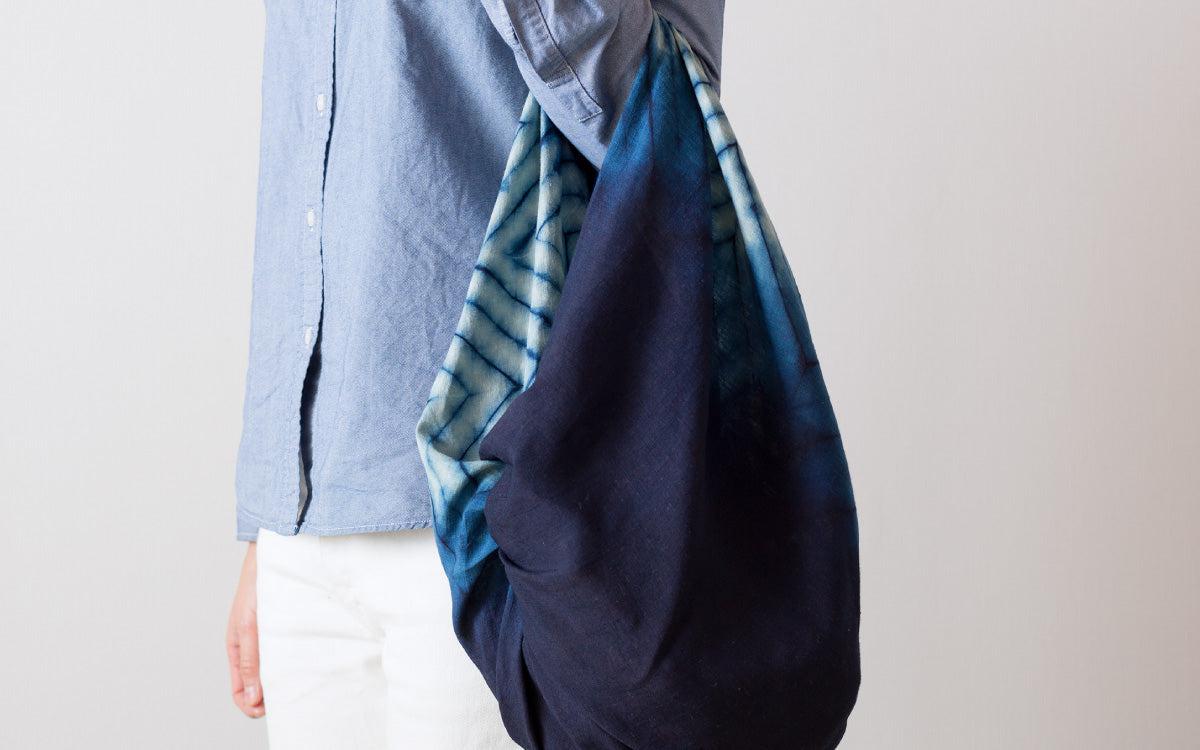
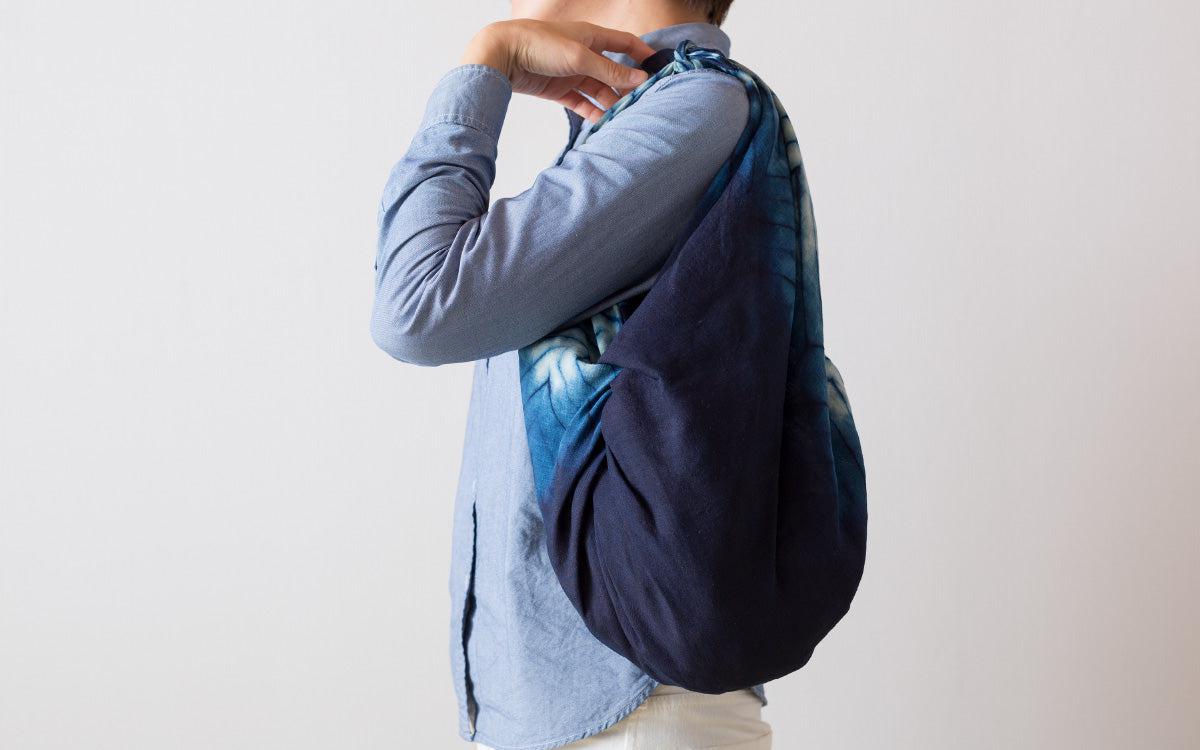
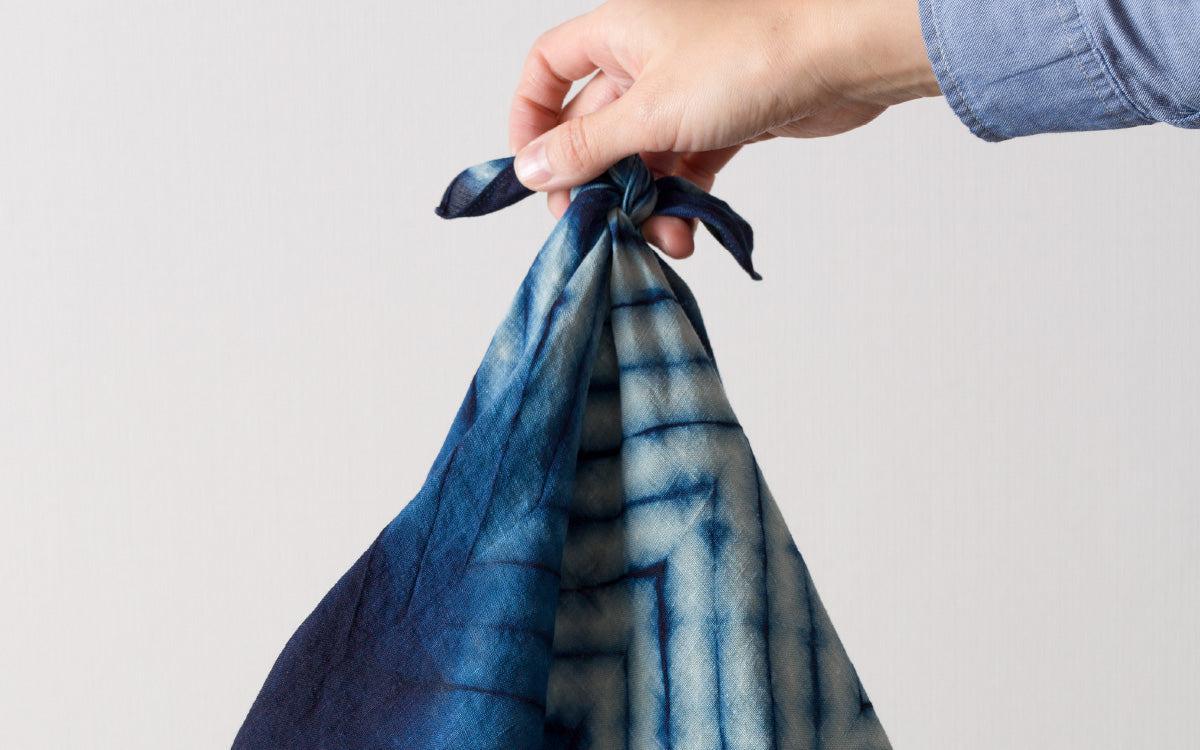

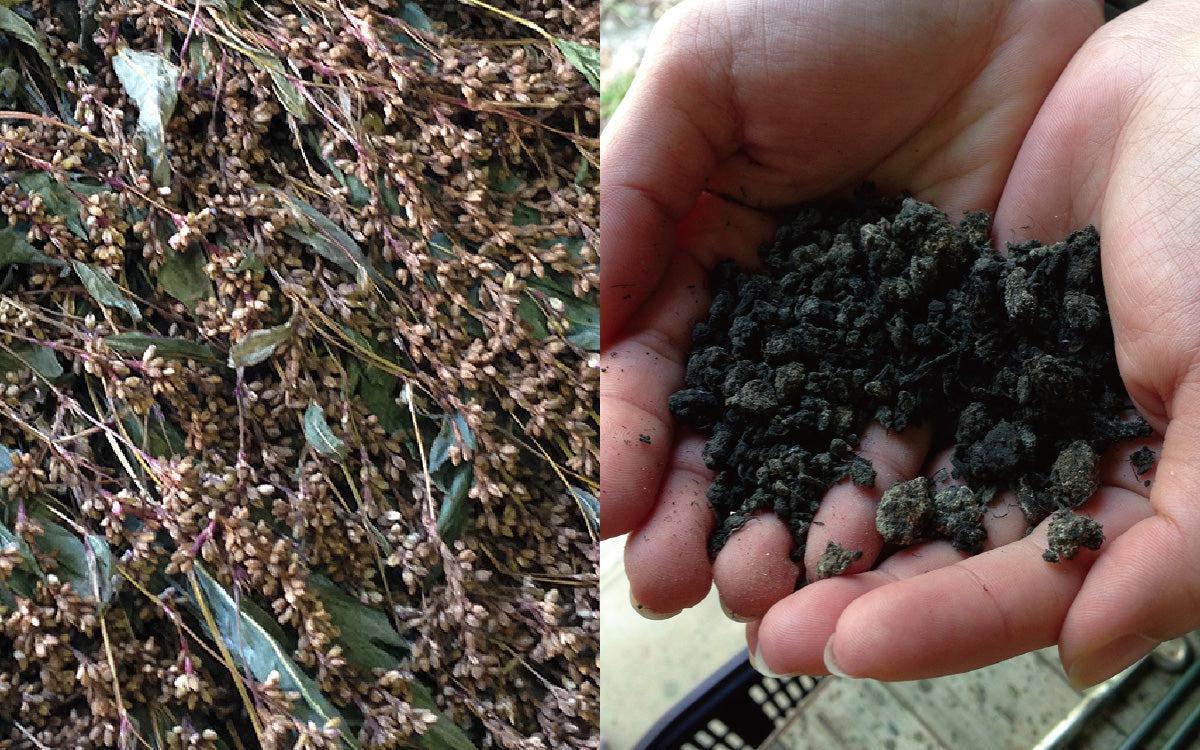
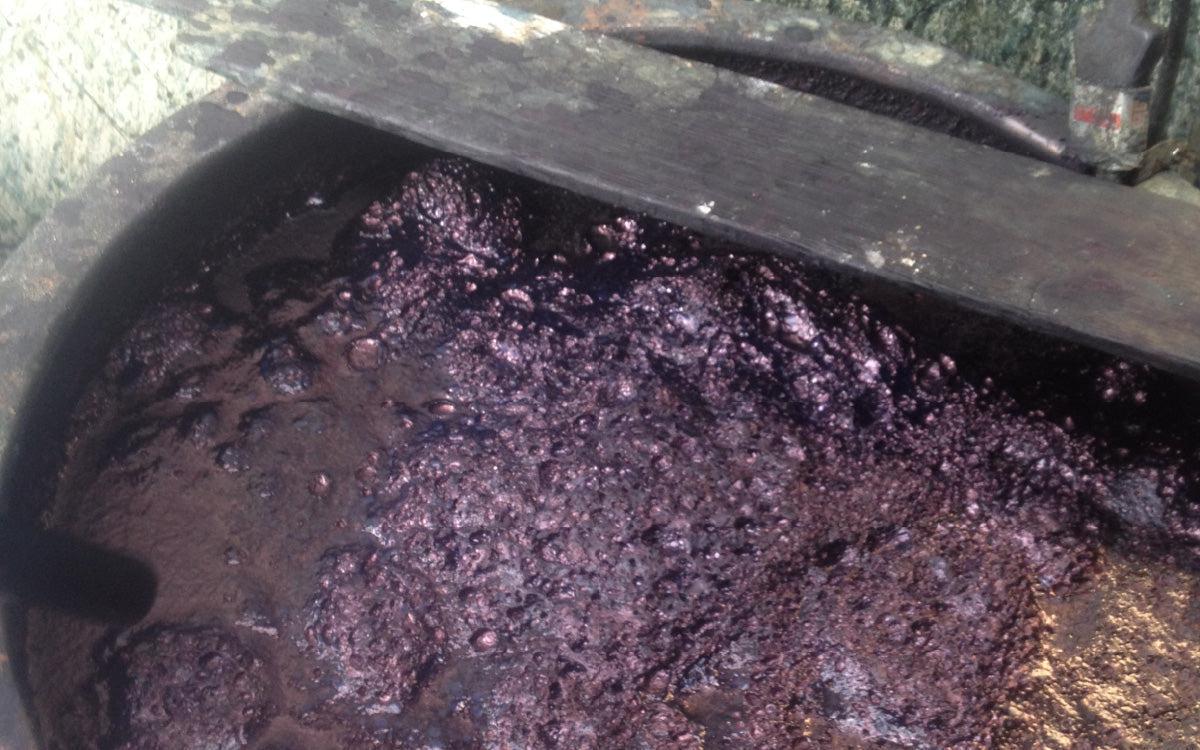
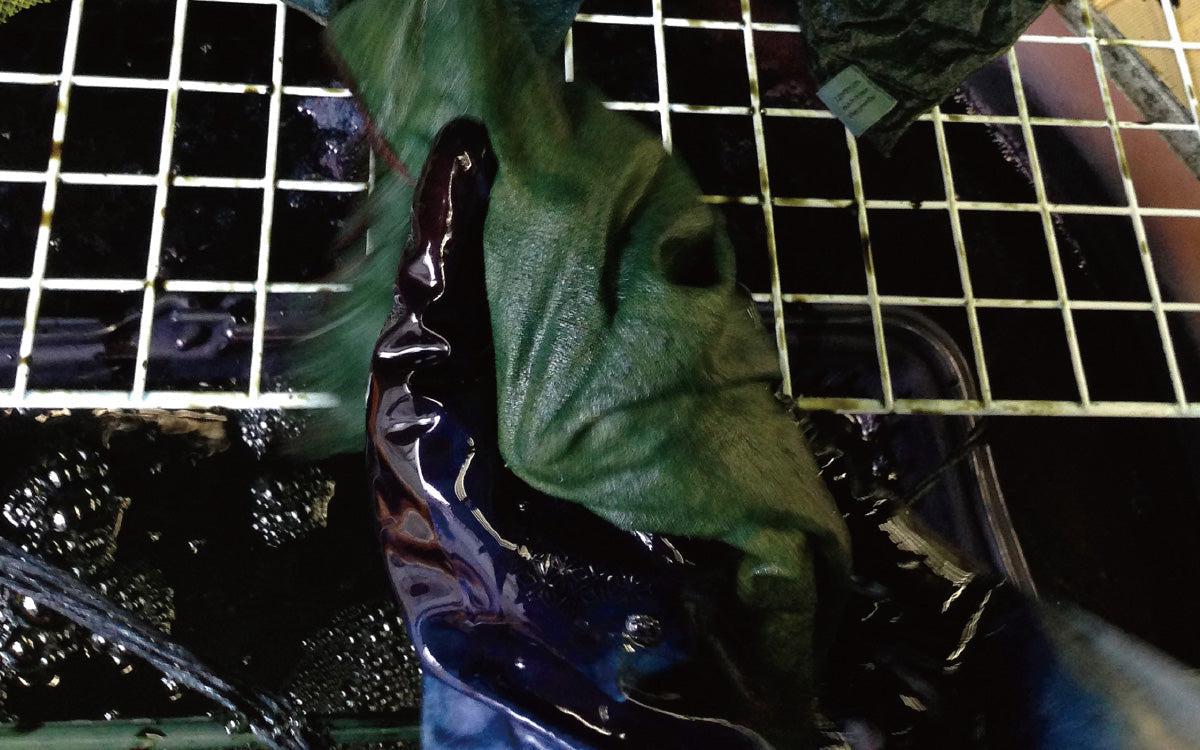
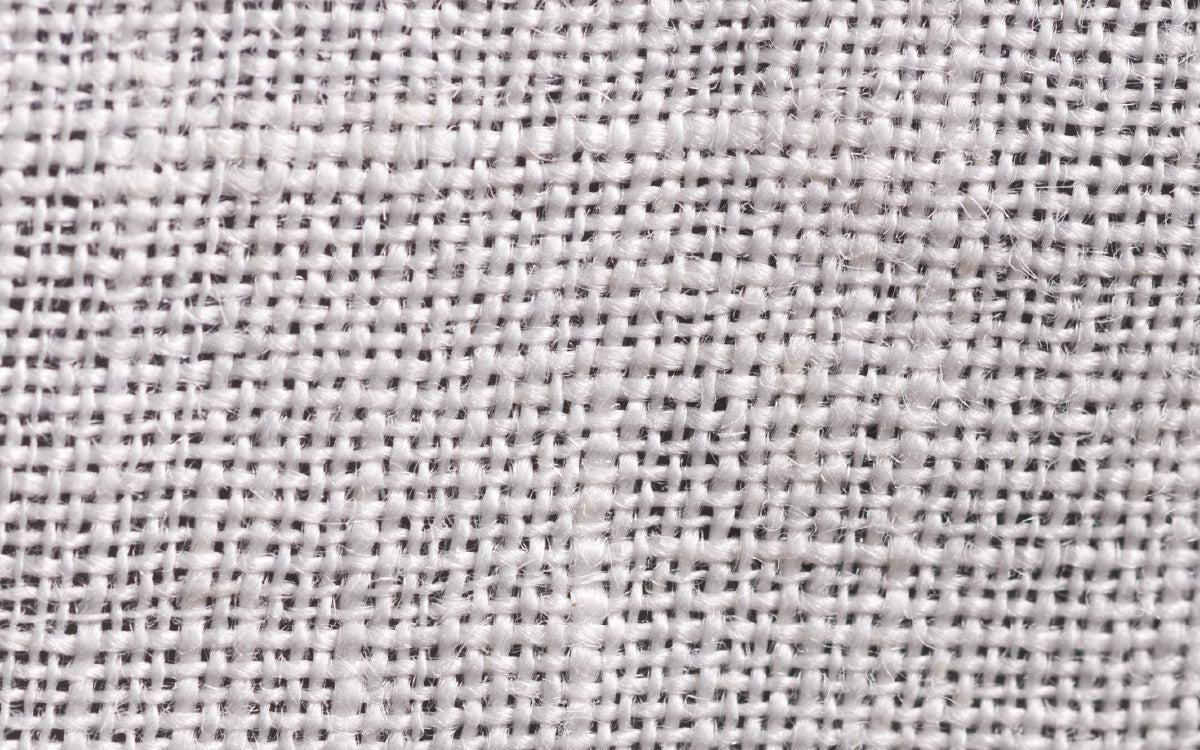
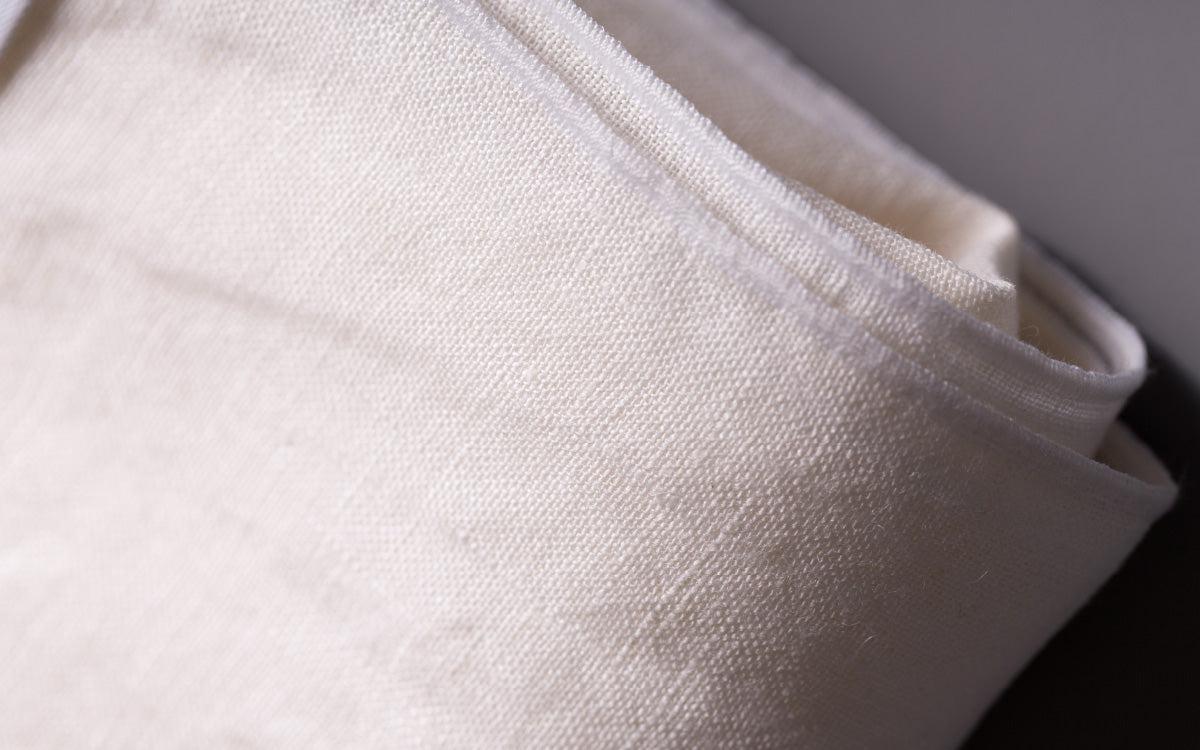
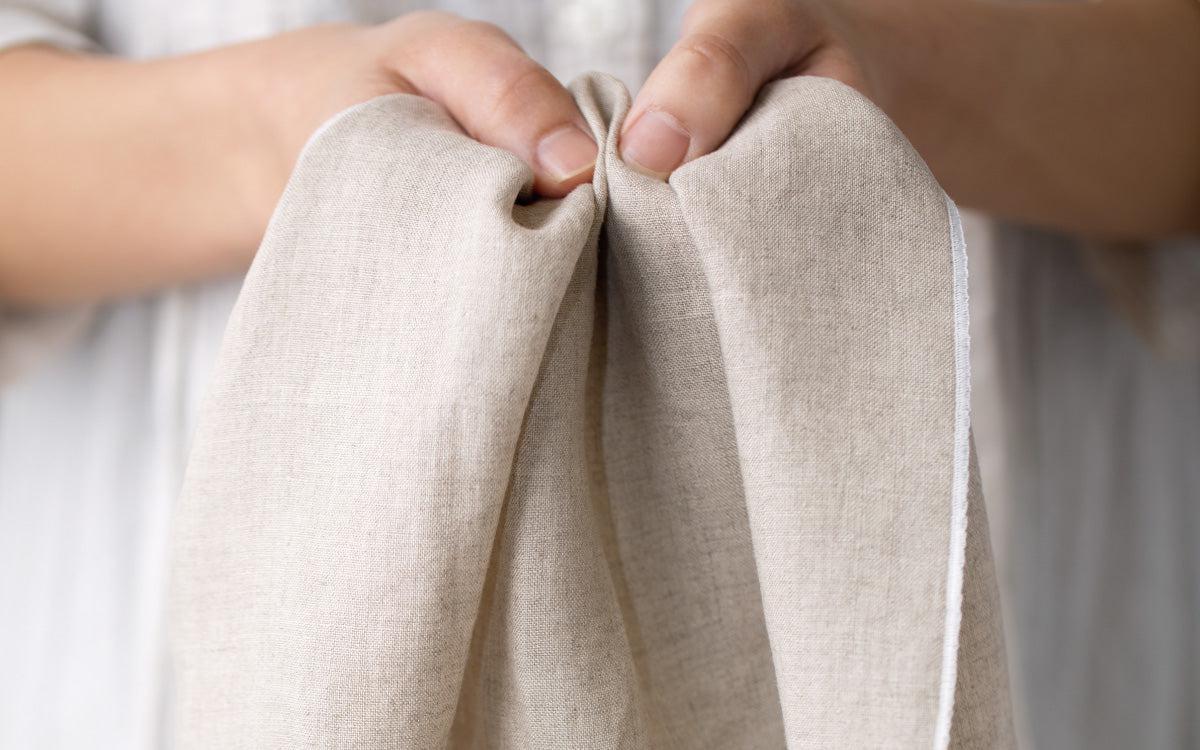
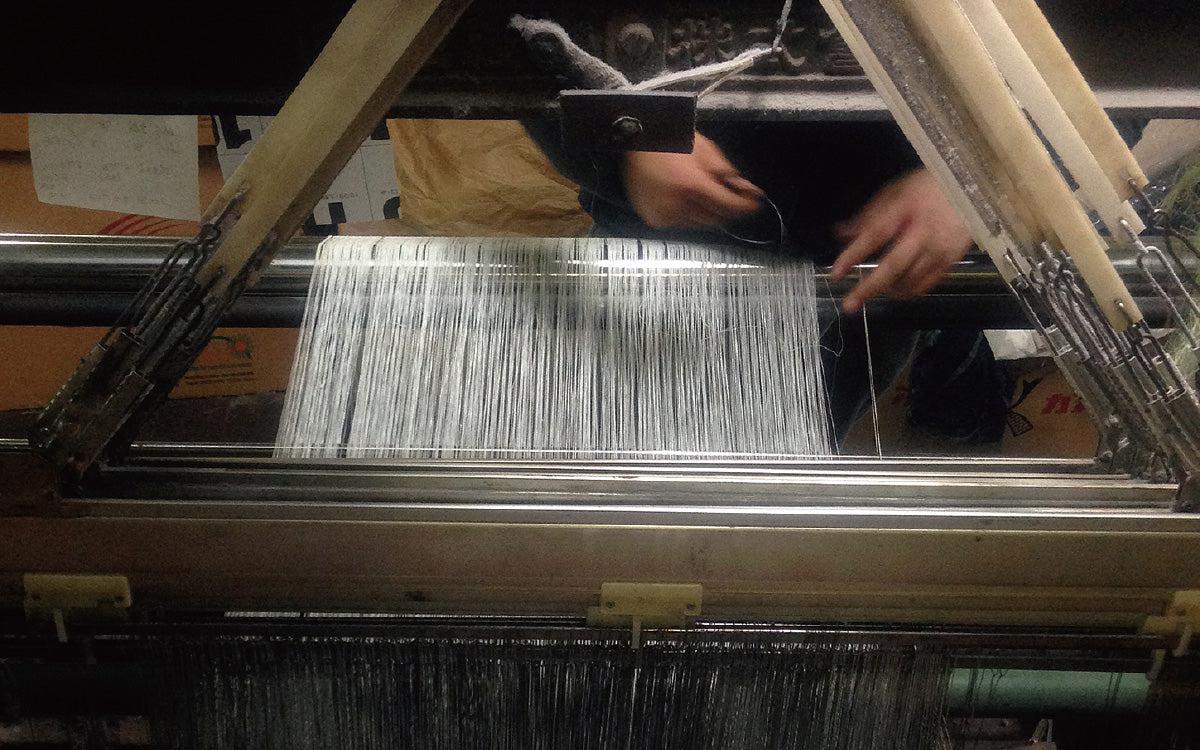
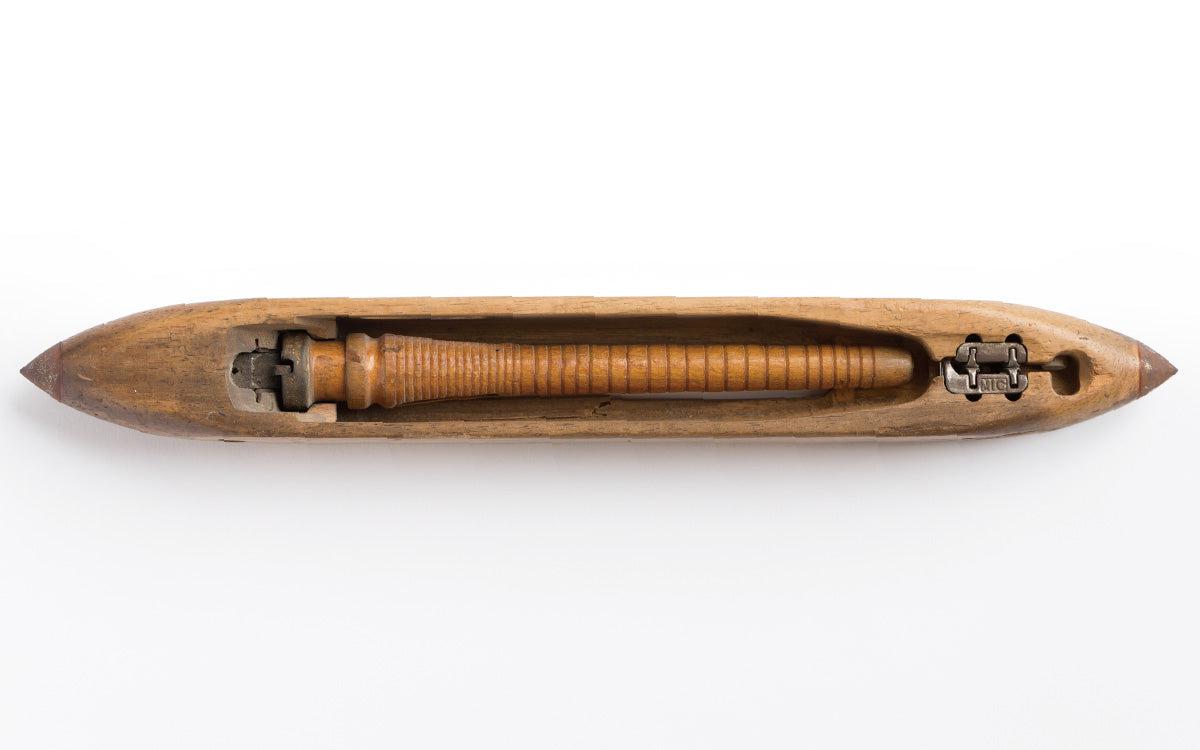